Chiller Maintenance
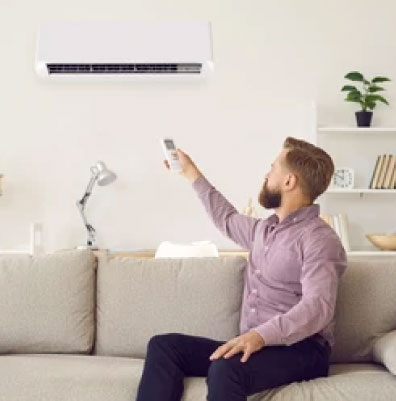
You need to maintain your chiller before the summer arrives. Click here to read the maintenance checklist by Dream Cool AC Service in Dubai.
Dream Cool AC Service in Dubai is the most experienced and unique in chiller maintenance. We provide suggestions and excellent pieces of work to our employees. While maintaining the chiller, every piece of equipment eventually experiences general deterioration and use. It contributes to the need to understand your commercial or industrial chiller thoroughly. Maintenance is necessary to ensure the longevity and effectiveness of large pieces of equipment. A content refrigerator equals a content bill. Using our chiller maintenance checklist to reduce equipment breakdowns and downtimes can be an excellent way to cut costs in your business. The tips below will help you maintain your industrial chiller and keep your business safe from catastrophic failures.
Chiller Maintenance checklist
When it comes to maintenance, keeping track of everyday activities is half the battle. The best way to monitor your chiller’s performance is to keep a detailed diary. The relevant data, including flow rates, operating temperatures, pressures, and fluid levels, should be recorded in these logs. To keep these figures current, several log sheets may be downloaded. Systems for remote monitoring are also widely used to support daily records on equipment. Since it is typically an automated system, it takes less time and may be updated as frequently as necessary.
The following items can be added to your general maintenance checklist to make sure you remember everything.
- Note the refrigerant and oil levels.
- Examining the fan control system
- Monitor evaporator water temperature differential.
- Measure the volts/amps of the condenser fan motor, if necessary.
- Check the evaporator water flow.
- Check the pressures in the evaporator and the condenser.
- Test the controls’ functionality.
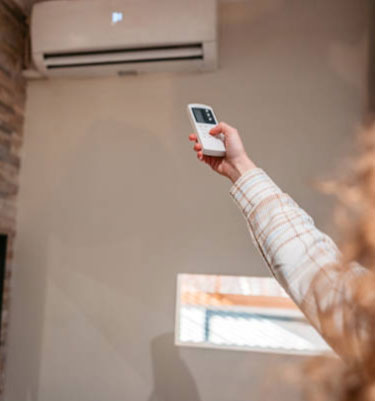
How to maintain a chiller
There are a few things that are necessary to maintain chillers.
Cleanliness of tubes
The performance of your industrial chiller can be significantly influenced by the tubes, which serve as the primary conduit for heat transmission in chillers. Impurities and pollutants may cause thermal resistance to increase. The opposition would reduce the chiller’s effectiveness of heat transmission by affecting the uniformity of approach temperatures. At least once a year, it’s crucial to brush these tubes. You can see issues before they arise if you have a robust monitoring system. You allow yourself to clean the pipes before they cause too much trouble.
Observer condenser water
For various reasons, keeping the condenser environment clean while maintaining boilers and chillers is crucial. Efficiency is decreased by both scale and corrosion. If the water is not adequately treated, both accumulate over time. Untreated may lead to more tremendous condenser pressures, hindered heat transfers, and irregular temperature and movement of the water. Chage the filters filters often, and periodic chemical treatments can help to keep the water pure.
Keep an eye on the condenser oil
It is normal to change the oil and filter after the first year of use while using a new chiller. Future oil change frequency is recognizeable by the oil analysis. The more frequently your system will need evolution, the dirtier it is. Furthermore, we suggest spectrometric chemical examination of this oil once a year. It will help you become familiar with your system and any potential problems. Learning how to handle different issues, from excessive water content to the size of the contaminants in the oil, is helpful.
Maintain the pressure of the system
Only low-pressure machines should use this procedure. It entails clearing out non-condensable gases from the system. These gases can be created on the low-pressure side of a chiller, where a pump or filter is located. These non-condensable substances can get inside the evaporators since they work in a vacuum. purge to ensure the air and moisture are at their lowest-ever levels.
Frequently Asked Questions
What is the problem of chiller AC?
The most common reason for chiller AC is the need for a high voltage. It will only provide the required temperature if an efficient voltage is provided.
How many types of chiller ACs are there?
There are two types of chiller ACs.
- Vapor compression chillers
- Vapor absorber chillers.
Which oil is better for chillers?
The chiller ACs are large and require colossal power to run. The best oil is that which absorbs the heat in a better way.
Why are chillers used?
Chillers are used to maintain the temperature of halls. In the winter, they are also used to provide heat to the space where they are installed.
What is preferable to run a chiller AC: gas or electricity?
Electricity is best for running the chiller AC because gas does not have that much power to run the chiller.
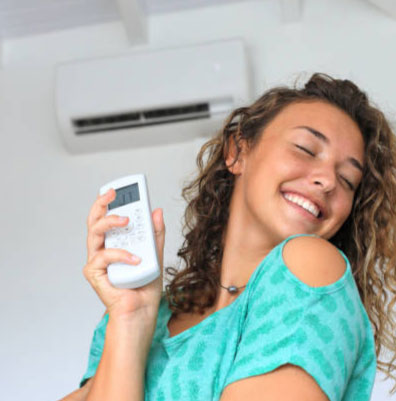